Summary of facts about EPS (expanded polystyrene)
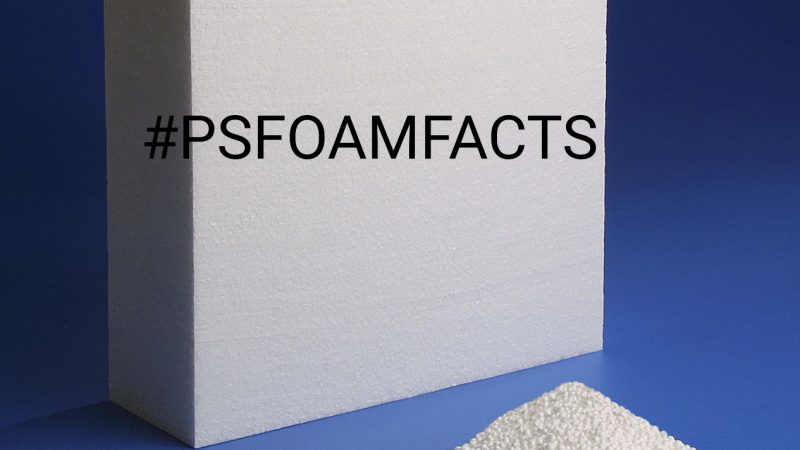
The aim on this page is to provide factual, well-documented information about EPS and its environmental credentials. The aim is to ensure balanced information about the manufacture, use and recovery from waste of EPS in the packaging and construction sectors. The purpose is to show customers, government organisations, NGO’s, other stakeholders and the general public that, by choosing or using EPS, you can be confident it is safe, complies with all relevant technical and environmental standards and can (and is) easily be recycled at the end of its primary use.
EPS, also known as expanded polystyrene, is an excellent material for packaging and for construction as it is a light yet rigid plastic foam with high impact resistance and very good thermal insulation. It is therefore used in a variety of everyday applications, where it protects buildings and transported goods. It is even used to protect humans as bicycle helmet and in car seats for babies.
However with increasing awareness of the environmental impact of human activities, it is important that we choose materials, which not only makes our lives easier, but also have a limited – if not a positive – contribution to protection the overall environment. Only through awareness can we ensure that we reduce our carbon footprint and protect our shared globe for generations to come.
This page is a one-stop, which summaries many of the key points made and documented on the rest of EPS-branchens website. Since EPS – expanded polystyrene – is used all across the globe, we have made this English version of the page as well. This is because not all decision-makers are located in Denmark, and we believe that this information should be available to all relevant stakeholders. Documentation on this page link to Danish sources.
What is EPS?
Expanded Polystyrene (EPS) is a rigid cellular plastic, which is found in a multitude of shapes and applications. It is used for – among other things – fish boxes, packaging for electrical consumer goods and insulation for building.
Those are the common uses, and those that will be elaborated upon on this page.
EPS is formed by expanding the raw material, which is polystyrene beads containing pentane.
EPS is similar to another polystyrene plastic foam, namely XPS (extruded polystyrene). However XPS is formed by adding gas (for instance CO2) during the extrusion process.
EPS Raw Material
Expanded polystyrene is made from expandable polystyrene beads, which are small sand-sized polystyrene grains containing an expansion agent (Pentane). The EPS raw materials are obtained from oil. In 2017 it was estimated that only 4 to 6% of all the oil and gas used in Europe is employed in the production of plastic materials. EPS accounts for between 3 to 4% of the plastic produced in Europe, which means that EPS uses between 0.1 to 0.25% of the oil and gas used in Europe.
If alternative materials were used for the same applications as EPS, then Europe would most likely need to use more oil and gas, which means a switch from EPS to alternative materials is likely to increase global CO2-emissions. This is due to EPS’ light weight and its effective insulation properties.
The manufacturing Process
Through a chemical process the oil is mixed with the pentane. Thereby creating the expandable polystyrene beads. These beads are then used in the EPS manufacturing process. The beads are converted into EPS in a four stage process.
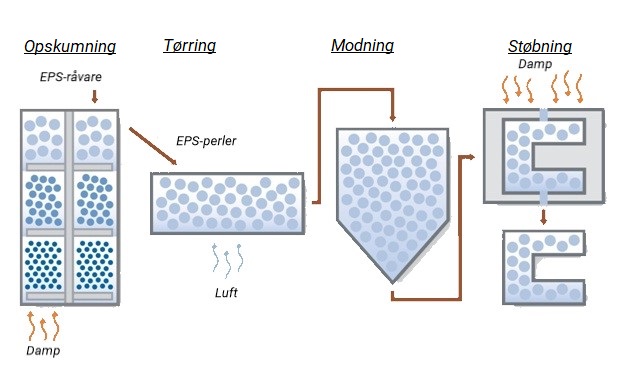
Stage 1: Pre-expansion
The EPS raw material is heated using steam in pre-expanders. The temperatures is between 80-100°C. The process releases some of the expansion agent is released and the density falls from app. 630kg/m3 to between 10 and 35kg/m3. During preexpansion process the compact polystyrene beads turn into cellular polystyrene beads with small closed cells that hold air in their interior.
Stage 2 and 3: Drying and Maturation
After the pre-expansion process, the recently expanded particles needs to cool down and mature. At the same time the beads are dried. This part of the process ensures that the EPS achieves a greater mechanical elasticity and improves the expansion capacity. Without this part of the process it would be impossible to ensure the mechanical properties in final product.
Stage 4: Moulding
At this stage of the process, the stabilised pre-expanded beads are transported to moulds. In these moulds the beads are again subjected to steam, which leads to addittional expansion, whereby the beads bind together.
Applications and Properties of EPS
EPS can be used for a wide range of different applications. These can however be categorized into three main categories, which are:
- Construction and insulation
- Packaging
- Other applications
Application as a materiale for construction and insulation
EPS is used in many different aspects of construction and insulation. For instance it is used in large structures such as roads, bridges, and railway lines. It is used as insulation in houses and other buildings. Some house are even built using Insulating Concrete Forms (ICFs), which are hollow EPS forms that are erected at the construction site. The forms are then filled with reinforced concrete. However unlike traditional concrete forms, ICFs are left in place as insulation for the constructed building. EPS has characteristics, which makes it ideal for use as a lightweight filler, insulation, as a lightweight filling material in roads, etc.
The following properties are important for these applications:
- Low thermal conductivity: Due to its closed air-filled cell structure that inhibits the passage of heat or cold, a high capacity for thermal insulation is achieved.
- Low weight: Densities of between 10 and 35kg/m2 allow light and safe construction works
- Mechanical resistance: EPS has excellent mechanical properties making it good choice for load-bearing roof insulation, sub-pavement flooring, road-building, as loadbearing insulation, and so on.
- Low water absorption: EPS does not absorb moisture and its thermal and mechanical properties are unaffected by damp, humidity or moisture.
- Ease of handling and installation: The material can be handled in the usual way. You are guaranteed a perfect finish. The low weight of EPS makes it easy to handle and to transport to site.
- Chemical resistance: EPS is completely compatible with other materials used in construction including cements, plasters, salt, fresh water, etc.
- Versatility: EPS can be cut into the shape or size required by the construction project.
- Ageing resistance: All of the properties listed above are retained over the whole of the material’s life and will last as long as the building itself. EPS is not altered by external agents such as fungi or parasites as they find no nutritional value in the material.
EPS packaging
Products of any shape or size can be packaged safely in EPS. The below examples are only some of the many different applications where EPS would be relevant to the industrial and food packaging sectors.
Packing Products
EPS is often the best packaging option for high value and/or heavy products. On the other hand moulded EPS may not be the ideal packaging choice for productss that have both a very low value and are very, very light weight. For such products EPS is often only relevant if using EPS packaging chips.
EPS packaging ensures complete protection and minimises the risk associated with transport and handling. EPS packaging is used These range from fragile pharmaceutical products to electronic components, electrical consumer goods, toys through to horticultural or garden products.
In the design phase it is ensured that EPS fits perfectly into automated production lines, which can include the packing of the product.
EPS packaging systems are often the best solution alternative in terms of cost, versatility and efficiency. It is easy for workers to handle with no sharp edges or staples and can work equally well with sophisticated machinery. Furthermore due to EPS enviromental profile EPS packaging systems often also has the best overall environmental profile, when looking at the materials life cycle, or from cradle to grave (or recycling as the case often is).
Food Packaging
EPS packaging is the best solution for keeping foodstuff, which need to be kept cold as part of a cold chain, fresh. This includes fish and shellfish, meat, fruit, ice cream.
When it comes to food packaging the key factor is food safety. If the product is insufficuetly protected or poorly insulated, it can arrive in a substandard condition. This condition could pose a serious health risk to consumers and it can cause serious wastage issues for supermarkets and food suppliers. EPS food packaging prevents this and avoids hazards, breakages and wastage in all the various stages of production and transport. Every day EPS packaging ensures that different foods reach retailers or the final consumers in perfect condition.
Hence EPS has important ecological benefits, as its capacity to conserve food helps to reduce wastage of food and guarantees food safety.
Other Applications for Moulded EPS
As a materiale EPS is very versatile. In fact it can be moulded into almost any shape. This allows for EPS to be used for a wide variety of substantially different purposes, such as:
- Snow sports helmets as well as bicycle helmets
- Infant car seats
- Air conditioning units
- Seating for sports – Formula 1 cars and para-Olympic sailors
- Frog houses and beehives
- Chairs
- Book covers
- Exhibition stands
- Even coffins
Properties of EPS when used in packaging or other applications
It is many of the same properties that make EPS relevant when used in packaging and in other applications.
- Shock absorption: The material has a high energy absorption index. This makes it the ideal material for protecting sensitive products during transport and storage. This unique level of protection makes EPS ideally suited for safety and sports helmets and for children’s car seats.
- Thermal insulation: Due to its closed cell structure, which inhibits the passage of heat or cold, EPS has a high capacity for thermal insulation. This protects products such as vaccines or other pharmaceutical items and food such as fish and meat from sudden changes in temperature.
- Low weight: EPS is 98% air making it the lightest packaging material available. This reduces the overall packaging weight and provides savings in fuel consumption — reducing the environmental impact of transporting products.
- Retention of vitamin C: When packed in EPS, fruits and vegetables retain their vitamin C content longer than food packaging in other materials.
- Resistance to humidity: The excellent mechanical and thermal properties are unaffected by humidity because EPS does not absorb water or water vapour.
- Compressive resistance: The unique ability of EPS to resist compression makes it ideal for packing large items such as cookers and washing machines. Not only does EPS protect them in transit, but they can be stacked in the warehouse, saving on space and without any damage to the items.
- Chemical resistance: Allows many products to be packed without the goods being affected.
- Hygienic nature: EPS is completely inert and innocuous, it meets all the food contact regulatory standards and can be used to package food or pharmaceuticals.
Life Cycle Analysis
A life cycle analysis is a technique intended to quantify the total impact of a product during its production, distribution, use and recycling, treatment or disposal. As individuals, and as organisations, all our daily actions have an impact on the environment. We use energy and resources, generate emissions into the atmosphere, pollute water and produce waste. One of the tasks of a responsible business is to calculate its impact on the environment and to find ways to reduce it.
However, some businesses use concern about the environment as a marketing tool and make claims that their products or materials are ‘environmentally-friendly’ or have a low carbon footprint. Responsible organisations will either conduct a thorough life-cycle analysis of a product, or calculate its carbon footprint using Carbon Trust methodology, (making their research public) before making statements of this kind
Reliable life cycle analyses will measure:
- Energy consumption
- Air pollution
- Water pollution
- Global warming potential
- Volume of solid waste
LCA’s of EPS environmental impact
When the choice is between single use items on should look at the overall environmental impact through an LCA. For instance replacing EPS/XPS cups with paper will require 12 times as much water and 36 times more electricity.
And a study in Journal of Cleaner Production found” this study has presented for the first time life cycle environmental impacts of most-commonly used takeaway containers: aluminium, EPS and PP. The results suggest that the use of aluminium containers leads to the highest depletion of elements and ozone layer as well as human, marine and terrestrial toxicities. The PP container is the worst alternative for the other seven impact categories considered. The best option among the three is the EPS container with the lowest impacts across the 12 categories.”
Northwestern University has also made a study of various single-use items and comparing these to multiuse items. They concluded that paper/cardboard is a poor substitute for EPS in an environmental perspective. The ideal choice is to bring your own cup – if you use it more than 20 times. Otherwise use polystyrene single use items.
Several other studies have found that plastic and EPS have a better overall environmental profile compared to other packing. See for instance “Plastic Packaging vs. Alternatives: Comparing Environmental Impacts” or LCA concerning TV/electronics packaging or here. Other LCA’s has been made for fish boxes with similar conclusions.
Other enviromental impact information
- Using oil to manufacture products in EPS can be an efficient use of this natural resource, for example: Each kilogram of oil used to produce EPS insulation panels creates a saving of up to wards 200 kg of oil used for heating residences and buildings (calculated over a 50 year period).
- Using EPS to package a product will result in a reduction in fuel consumption compared to other materials.
- EPS is a fully recyclable material, which is in fact being recycled on every inhabited continent. This is because EPS is easy to identify and worth collecting (1 ton of compacted used EPS easily sells for 450 euro).
Styrene
The monomer styrene, used in the manufacture of expandable polystyrene, has been manufactured for more than 60 years and is used for a wide range of plastics and plastic products. For instance Styrene is also used in the production of wind mills.
Styrene also exists naturally and can be found in many foodstuffs including strawberries, beans, nuts, beer, wine, coffee beans and cinnamon. Exhaustive research by Harvard Center for Risk Analysis at the Harvard School of Public Health into the health effects of styrene has shown that although high exposure levels can be dangerous, like most chemical products, styrene is perfectly safe for normal use. Based on the current EU classifications, styrene monomer is considered to have low oral toxicity, and is not classified in terms of carcinogenicity or mutagenicity.
And a study by Aarhus University and COWI for the Ministry of Environment and Food of Denmark concludes that EPS is non-toxic as a material.